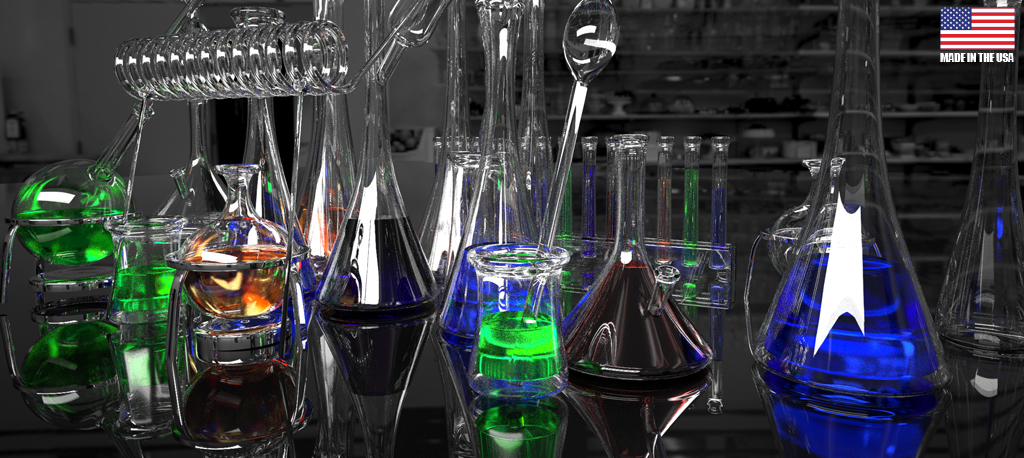
Introduction:
The total annual cost of corrosion in the oil and gas production industry is estimated to be $1.372 billion, broken down into $589 million in surface pipeline and facility costs, $463 million annually in downhole tubing expenses, and another $320 million in capital expenditures related to corrosion. The damages caused by exposure to corrosion can affect all of your components and potentially produce costly failures which inevitably lead to lost production. Typically, the corrosion is the result of the steel’s exposure to gaseous or liquid hydrogen sulfide [H2S]. On a molecular level, hydrogen ions work their way between the grain boundaries of the steel, recombining into molecular hydrogen [H2], taking up more space and weakening the bonds between the grains of the steel. This formation, hydrogen embrittlement, can cause sudden metal failure due to cracking, reduced ductility and stress fissures. As the concrete encasing the bore flexes with the variation of pressure, movement of the bore and temperature changes, gaps, cracks and fissures form allowing the introduction of oxygen and hydrogen which initiates oxidation or corrosion.
Solution:
As the StimMax Corrosion Inhibitor(s) is introduced into the well, the liquid phase is absorbed into the metal surface forming a protective layer that physically prevents corrosive chemicals such as water, chloride ions or hydrogen sulfide from penetrating the metal surface. The unique chemical construction of the product produces a polar head group and a hydrophilic tail. The head groups are designed to interact with iron atoms on the surface while the hydrophilic tails attract liquid hydrocarbons, forming an oily film, which further prevents the corrosive aqueous phase from penetrating the metal surface. The unique blend of overlapping charged particles in StimMax Corrosion Inhibitors have the ability to “heal” existing pitting and scaling by filling in and sealing these erosions. At the bottom of the wellbore, the ambient temperature and pressure converts the product into a fog or vapor phase that will naturally migrate outward and upwards, healing, sealing and coating both sides of the exposed metals. The advantage of the product when it converts to the gaseous stage is that the volatilized molecules can reach hard-to-reach spaces and when they reach the metal, StimMax Corrosion Inhibitors attach to it by the active group, neutralizing damaging acids into a harmless sulfur compound that goes away.
Results:
Bio-based, bio-derived and biodegradable, StimMax Corrosion Inhibitors are safe for the environment as well as the oil field operators; and is a clean way to address costly issues without the use of deadly sulfides and Sulphur or dangerous acids that may also contaminate the oils and gas. By creating a sub-micron, porous molecular basket that captures and neutralizes the corrosion causing gasses, acids and materials, the life of the bore is extended by a minimum of 50 years. The anaerobic environment that breeds H2S and other damaging gasses is effectively neutralized while the self-healing properties of the product provide long term protection.
StimMax Corrosion Inhibitors are the “natural” choice to “Seal, Heal and Protect the Steel!”
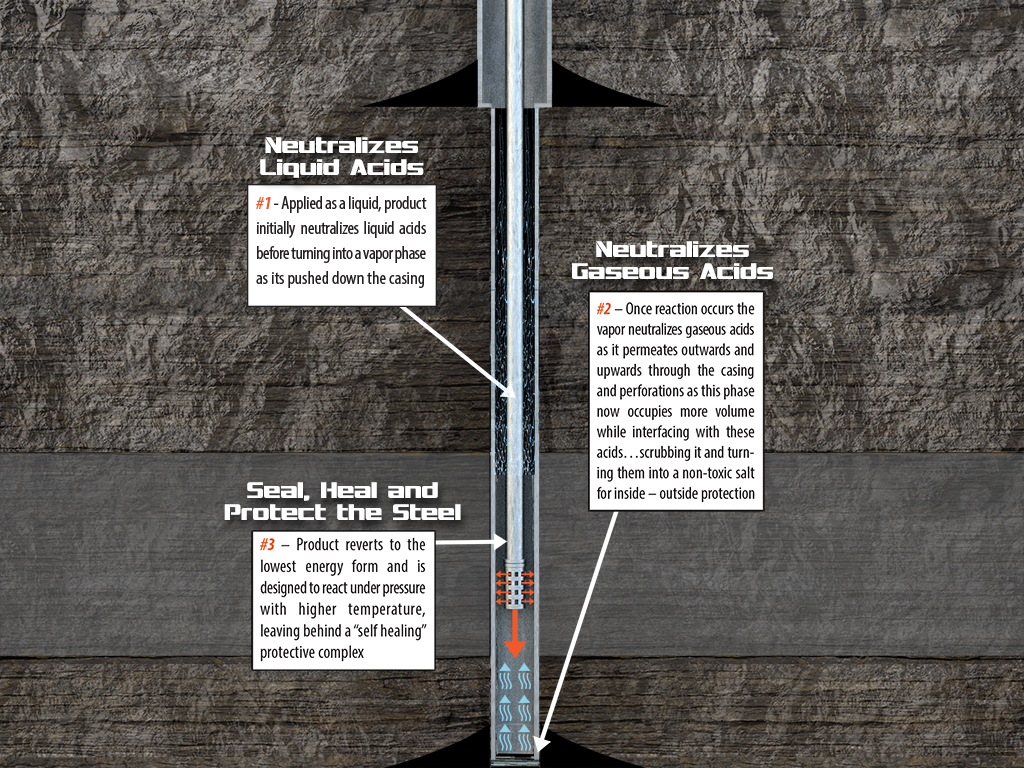
StimMax Corrosion Inhibitors will also perform on the external surfaces of the casing in the following ways:
- First, if the cement is completely adhered to the casing, then there will be no corrosion. This most likely will never be the case as the cement around the casing will
- Have cracks and voids
- Naturally begin to separate from the casing
- Curing cement will have fissures and capillaries
- The cement is not a solid object, but is permeable by gas or vapors
- Once the liquid becomes a gas due to ambient pressure and temperature, it will penetrate the perforations and begin its natural migration upward, finding openings, fissures, cracks and voids…coating and healing the casing as it moves up.
- This is not an instant process as the gas must move upwards through very tiny openings, but this gas, now at a nano-metric scale, is the only product that can both penetrate these openings and migrate up the casing.
- The non-conventional nature of this solution is supported by the simplicity of its design.
Corrosion Test Results | Corrosion inhibitor Toxocity